QUICKSILVER ™ RIG PACKAGE
- By Joe Nichols - STRIKER President
- •
- 16 May, 2019
- •
The Idle Aging Rig Challenge
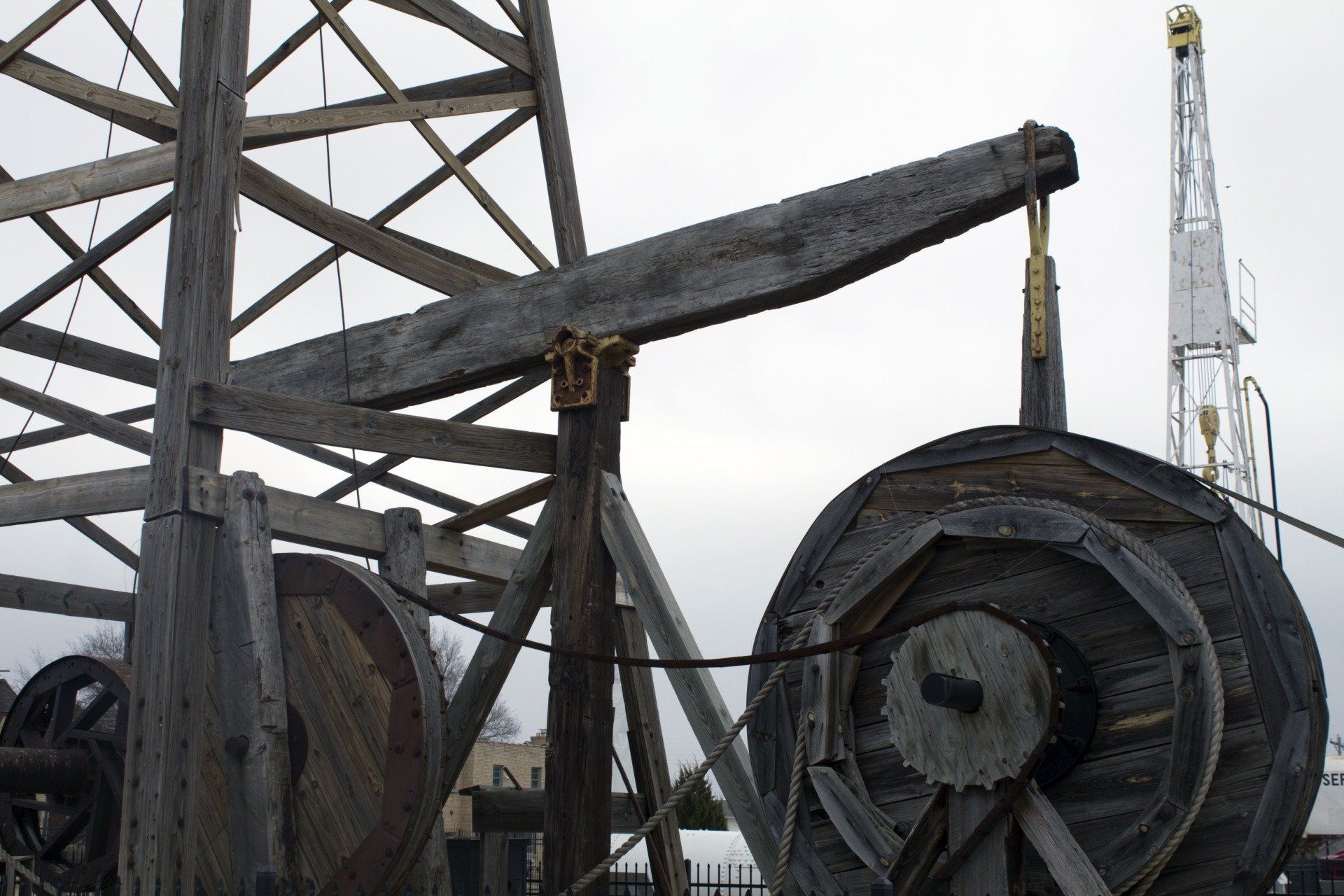
DC Magazine
Day rates remain low and rig capability requirements from Operators continue to increase to drive efficiency in the drilling operations. Wells continue to get deeper (longer reach horizontals), requiring increased racking capacity, and larger capacity mud systems able to pump higher low rates as well as higher pressure. Larger pads with more well heads require contractor’s rigs to walk greater distances and move in both the X and Y directions. Walking further also requires extensive cable management and other upgrades to maintain efficiency of the rig. Expectations are also that cycle times for walking is short and the rig is capable of walking with a full setback load over wellheads and not having to manually handle pipe racks.
Our clients are always faced with a few choices with an idle aging rig fleet: upgrade or build a new rig. The reality for our clients that operate 10-50 rigs is that they don’t have the CAPEX to hedge building or upgrading a rig until securing an operator contract. Building a new rig is an attractive option, but often the most expensive choice in addition to pushing lead times outside of the demands of most drilling current drilling contracts. At Striker we understand more than just engineering and helping bring existing fleets up to current and future requirements. Striker understands the business of contract drilling. One of Strikers largest and most successful projects was the rebirth of Independence Contract Drilling (ICD’s) aging Quicksilver™ Fleet of rigs into the modern contract winning Shale Driller Fleet. This is our story.
It was December 2 of 2011, the WTI oil price was $100.96 per barrel, drilling contractors and the entire oilfield services providers were scrambling to capitalize on the booming market. Independence Contract Drilling was one of these contractors, armed with a 1600 HP Quicksilver™ Drilling System and the capital to build two more. As a young contract drilling company in a very competitive market, it became apparent to compete in this industry ICD needed a more advanced, marketable rig design. The minds at Striker were given the opportunity to work very closely with ICD to modernize their rig design. Striker started by identifying and addressing challenges with their 1500 HP QuickSilver™ land drilling rig.
Where was the industry headed, how can we keep up, and how can we get ahead?
The Quicksilver™ in its day, was a very formidable design. The Quicksilver™ rig was a fast-moving rig in its day, with the ability to rig down, and rig up 100 miles away in 48 hours, all without the use of cranes. It utilized a two-piece substructure that raised vertically to a 22’-0” drill floor height, and a 136’-0” mast that telescoped in to be transported as a single load without disassembly or un-reeving the travelling assembly. All of the backyard skids were tailboardable, and anything that needed to be raised into operating position could do so hydraulically. Being a fast moving rig was a huge advantage and for a long time was well sought after and utilization of the Quicksilver™ rig design was high. Fast forward 10 years and the demands of operators started changing. It was getting increasingly more difficult to keep these rigs utilized due to the newer, more capable rig designs that were coming to market.
Some of the challenges the aging rig design faced were as follows:
- Drilling programs called for larger Blowout Preventors and taller stacks. Quicksilver™ rigs could not bid these contracts as, the rig’s 18’-0” working clearance was too short for what was required.
- Drilling multiple wells on a single site, or “pad drilling” as this has come to be called left the Quicksilver™ unable to keep up with newer rigs that were walking capable. Its quick moving design was an advantage moving from site to site, but slower for on-site moves required for Pad drilling programs.
- During this time the number of directional wells surpassed the number of straight wells, opening the gate for wells that were both longer and deeper. This required that rigs are able to rack far more pipe than they were originally designed for. The old rule of thumb that your rig should be able to rack 10X the horsepower of the drawworks no longer applied. The Quicksilver™ racked 14,400 ft of 5” drillpipe, but wells were now requiring much more pipe than that.
- Deeper wells require more out of the mud system, more pit volume and higher discharge pressures from the mud pumps, another area of attention and upgrades.
- Many competing rigs in the 1500 HP class were already utilizing 500 ton top drives, with increased torque capabilities and lifting. However the rig’s 136’-0” mast clearance height wasn’t enough to house anything longer than the 350 ton top drive.
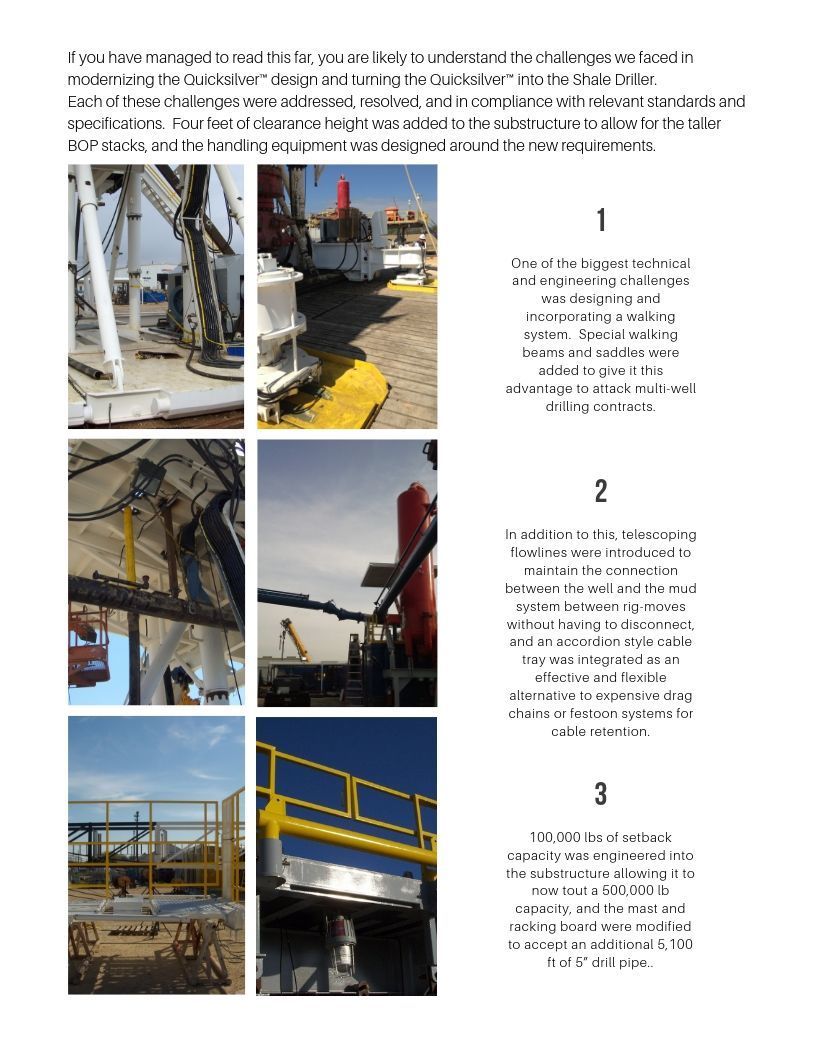
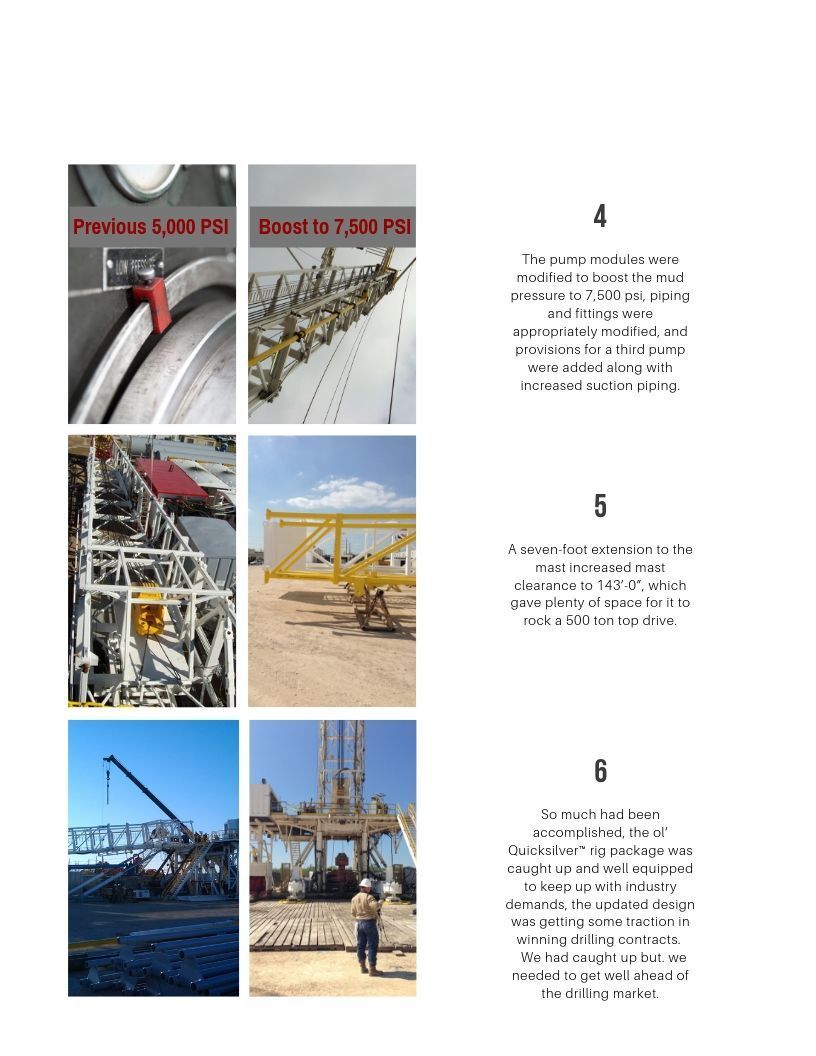
Momentum for ICD favored the efforts in creating a new substructure that is designed with the intent to be a walking rig. A timeline had been established to have the new product designed, built, and ready to spud in an 8 month time period, so STRIKER got to work. The result was a Single-Load Substructure that drastically reduced rig-up and rig-down time, as well as reduce transportation costs generated during rig moves. Imagine being able to tailboard your entire 1500 HP rig’s substructure onto a truck in a single operation, and how much time and money that would save. It interfaced seamlessly with the triple-telescoping mast design, and the structural geometry allowed the mudboat and mast dolly to be left behind during walking operations, utterly simplifying the process. The walking system was also an easy-install as the provisions were engineered into the base beams, along with the capability to walk over 4 ft wellheads (something that the Quicksilver™ design inherently could not do, all wellheads had to be below grade). From dream to spud, this rig was the first of many of its kind and was going to work within 8 months from the design inception.
Fast forward to 2019, many advantages of the Quicksilver™ design have become obsolete and less competitive in the crowded contract drilling market. Good bones of the design allow the Quicksilver™ rig to be upgraded and modernized through careful planning and engineering. Thank you for taking the time to read this article. To download the entire article, please click here.
www.strikerds.com
Contact us today!
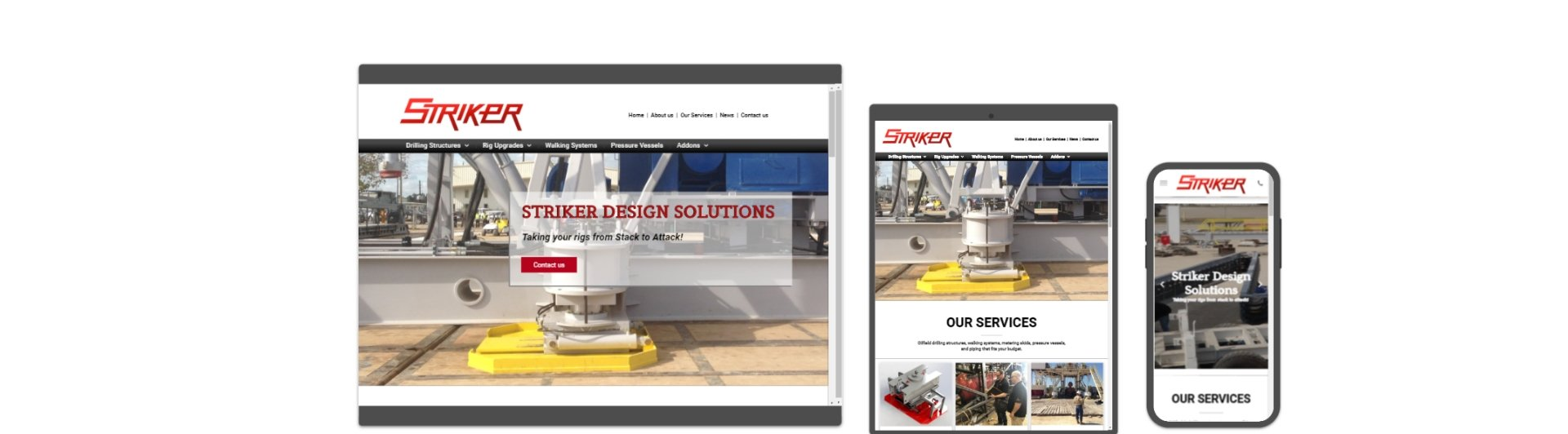
Released!!
Our brand-new and upgraded website is up and running, listing our services, products and our news!
It is all about oilfield drilling structures, walking systems, metering skids, pressure vessels, and piping that fits your budget.
Striker is on a mission to help take idle rigs with good iron into competitive, contract winning machines.
Most notably was the transformation of ICD’s Quicksilver fleet into the ShaleDriller fleet.
According to Drilling Contractor Magazine between 2017 and 2018, 805 rigs have been removed from service. Could breath some new life into that iron and put them back to work.
The launch of Striker’s new website highlights what is possible in making old rigs competitive again.
Check it out @ www.strikerds.com
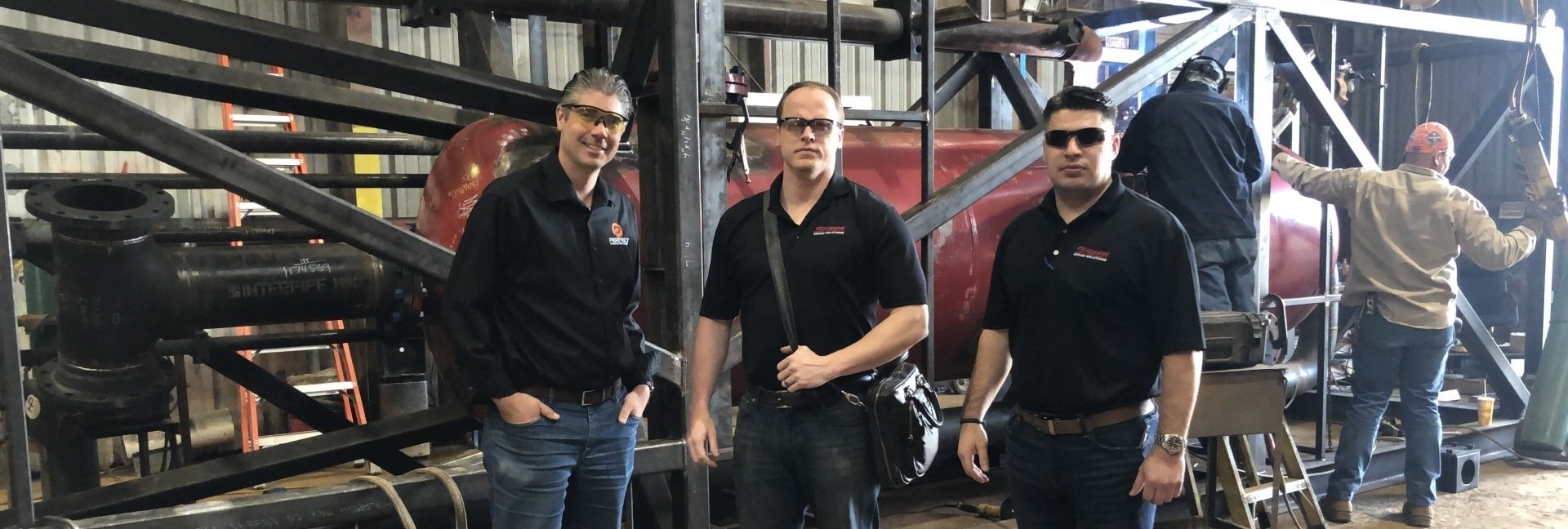
Perfect Consulting Group would also like to welcome Striker Design Solutions as our latest client. Striker provides expert engineering services and turnkey custom solution to our clients in the Drilling and Custom Production Equipment market.
Most notably Striker designed and delivered many of the modernization components including walking and auxiliary systems to turn ICD’s aging Quick Sliver fleet into the modern and highly utilized ICD Shale Driller fleet.
Perfect Consulting Group is helping Striker to update their marketing materials, new website (coming soon) expanding market reach, introducing contractors and partners as well as making it easer and faster for drilling contractors and Operators get the solutions they need through modern commercial engineering practices.
If you have a project that needs excellence in engineering, contact STRIKER:
sales@strikerds.com
www.strikerds.com
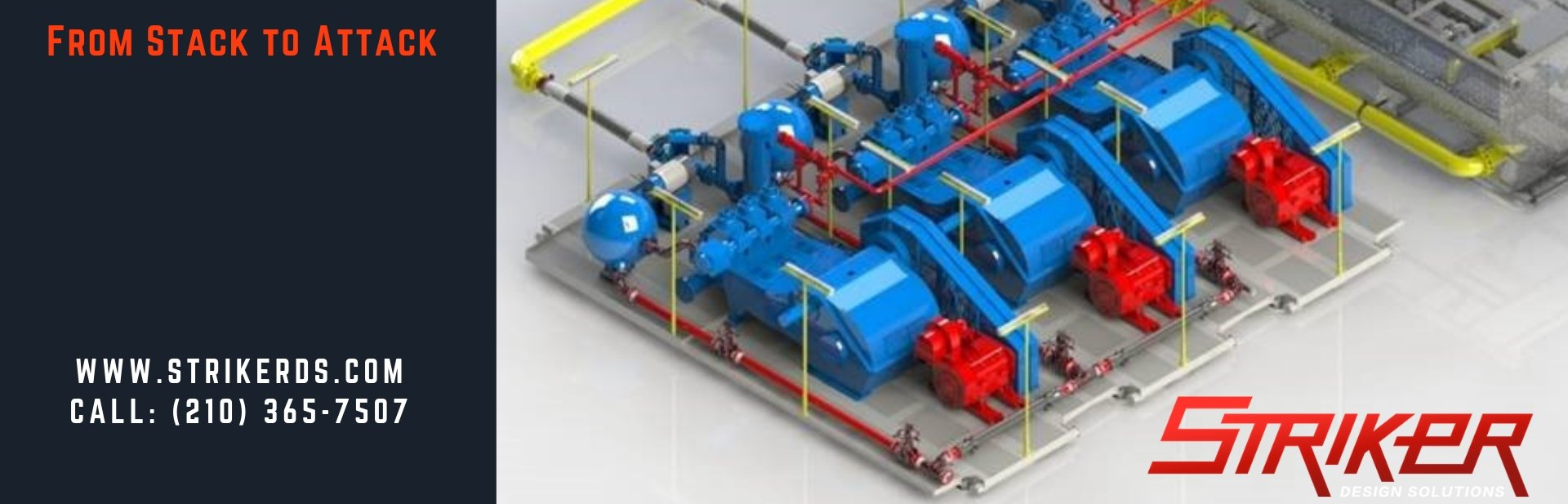